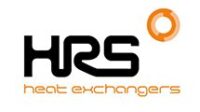
Member press release (Opinion piece) – The importance of heat exchanger aftercare
By Matt Hale, International Sales & Marketing Director, HRS Heat Exchangers

When considering the purchase of a heat exchanger or processing system, there are many considerations to be made, including the suitability of the equipment for the task in hand, the capital and operational costs, how easily the equipment will fit into existing systems and facilities, and many other small concerns. What is not always considered is the follow-up service and aftercare, both during delivery and commissioning, but also further into the future.

The term aftercare can be applied to any support obtained from the supplier once the order has been agreed and can therefore include initial start-up services such as commissioning and installation. Depending on the nature and size of the project, these will often be carried out by the supplier in conjunction with the client’s own engineering team and/or third-party contractors. HRS can either carry out commissioning and installation directly using its own staff or supervise the installation of its components by others – something that is necessary whether you have bought a bespoke engineering solution or a pre-designed system. Over the last two years, the Coronavirus pandemic has seen an increase in the use of IT and communication systems to supervise commissioning remotely, a solution which allows for efficient and timely installation while limiting travel and contact.
While correct installation is essential to increase the lifetime of the system and ensure its correct functioning, there are other support services which clients should expect from their equipment suppliers. These include initial aspects such as the provision of training and documentation for both operation and maintenance.

When equipment is fitted with a remote access and monitoring system, the manufacturer can access key information and metrics and, when necessary, log on and discover any potential issues and quickly identify their resolution. Using the manufacturer’s design expertise and technical know-how can save time and money by identifying problems and solutions quickly and without incurring costly site visits.
A reputable manufacturer will also offer expert insights into the latest technological advancements that could benefit users’ systems process and operational costs. For example, a performance audit allows the manufacturer’s engineers and designers to analyse the performance of the equipment and offer guidance on how to improve, properly maintain desired conditions or reduce costs. In addition to condition monitoring, this will provide fact-based insights into the performance of the equipment to prolong service life and help to plan maintenance.
This will also allow the supplier to suggest appropriate upgrades which will improve system performance, increase capacity or operational efficiency, or lower running costs. In certain cases where other factors are of paramount importance, such as the footprint of equipment, space saving solutions can be implemented.
Maintenance needs can vary depending on the type of equipment or products being processed and the required design conditions. Therefore, when selecting a heat exchanger supplier, it may well be useful to ascertain the range of maintenance services which they can offer to help keep equipment running smoothly, including preventative maintenance and servicing, holding reserved stocks of necessary spare parts, and exchanging components where necessary.
Today’s global business structures mean that the location of manufacturing plants is not an issue when it comes to choosing an equipment supplier, and as such you should look at a supplier’s capabilities to support you both locally and remotely.
– ENDS –
For UK media enquiries about HRS Heat Exchangers please contact:
Yenni Maelianawati,
Senior Marketing Manager, 3 Abloy House, Hatters Lane, Watford, Hertfordshire, WD18 8AJ
Tel: 01923 232 335
Direct Email: yenni@uk.hrs-he.com
Email for publications: info@uk.hrs-he.com
www.hrs-heatexchangers.com
About HRS Heat Exchangers
Located in the UK, HRS Heat Exchangers is part of the HRS Group which operates at the forefront of thermal technology, offering innovative heat transfer solutions worldwide across a diverse range of industries. With 40 years’ experience in the food, pharmaceutical, environment, and industrial sectors, specialising in the design and manufacture of an extensive range of turnkey systems and components, incorporating our corrugated tubular and scraped surface heat exchanger technology, HRS units are compliant with global design and industry standards. HRS has a network of offices throughout the world: Australia, Canada, New Zealand, UK, Spain, USA, Malaysia and India; with manufacturing plants in the UK, India, Spain and Canada.
Release issued by GloHouse Media:
Bev Small, bev.small@glohouse.co.uk, Tel: 01223 872239 / 07901 841491